R. Resource Usage Is Too High (Headcount Reduction) Overview Unfortunately, this project gets identified on a regular basis early in a deployment. Fortunately (in most cases), a quick rethink shows that the issue is not one of too many heads to support the revenue generated, but too little revenue generated for the headcount. It is always better to grow out of this problem than to shrink headcount. Often an investigation of delivery performance or capacity can identify a better road. Traditional thinking is often based on a shortsighted slash on the one resource that might give a significant return. Nevertheless, there are legitimate reasons for doing this type of project, especially in industries such as healthcare where there is a shortage of key skills and we would like to reduce in one area to reuse/expand in another. Finally, there are those (albeit rare) cases where there truly is a burden of a headcount that is too high. Examples Any process where there is desire to reduce headcount, whether it be because of low availability of certain skills, high turnover problems, or just a desire to cut high labor costs. Measuring Performance The usual headcount costs are the best measure to use in this type of project (i.e., labor costs, salaries, benefits, etc.). It is also often worth considering the Total Work Content as a measure of performance because headcount is based directly on this. Tool Approach The roadmap approach in this problem is primarily based on examining resource activity to reduce work content of NVA activities. 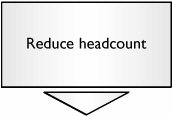 | It might at first glance seem that cutting heads should be the last step in the process. In fact, it would be if the resource that was being cut were not people. If management is absolutely set on cutting resources it is always better to cut first and then recover with a project, rather than vice versa. If the cut were made after the project, it would effectively sound the death knell for the program as a wholeLean Sigma would be linked forever with headcount reduction and no one would want to be involved in projects thenceforth. It is far better for the project to be seen as a huge help after a headcount reduction to make things workable. | 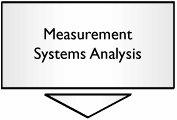 | For our headcount measures (whatever we choose), we will need to look at the validity of the metrics; a sound operational definition and consistent measure versus a detailed investigation of Gage R&R will suffice. For more details see "MSAValidity" in Chapter 7, "Tools." | 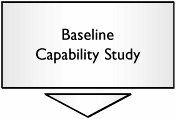 | Take a baseline measure of costs. It is highly likely that historical data is available and is fit for the purpose. |
After we have a solid baseline, the project can move relatively quickly and is a good kaizen opportunity. 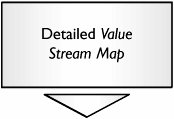 | Construct a rigorous Value Stream Map including all the detailed steps for the Primary Entity as it progresses through the process. Ensure that time is spent mapping the (secondary) resources (i.e., the people, as they are involved in the process). | 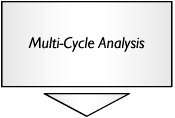 | Apply a Multi-Cycle Analysis to the Value Stream Map to identify where the resource time is being spent along with an indication of variation in times. From the data also identify the Total Work Content in the process. | 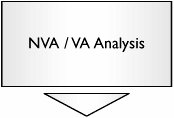 | Use the Value Stream Map and data from the Multi-Cycle Analysis to identify NVA activities. The Team should spend time brainstorming action ideas to eliminate NVA activity in the process, which will in turn decrease the Total Work Content. | 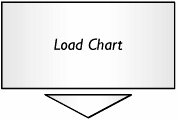 | A Load Chart for the process will show Takt Time versus Cycle Time. For more details see "TimeTakt Time" and "TimeIndividual Step Cycle Time" in Chapter 7. This is a crucial element in the picture. It will only be possible to cut headcount down to the point that the number of resources meets the Total Work Content for the level of demand. Any lower and the process will not meet the pace of customer demand. |
At this point, the Team should have a reasonable understanding of where the resource time is spent and the process shouldn't have operators spending time on too many NVA activities. To take this further, the Team should look to other Problem Categories for solution. Examine resource time to further identify 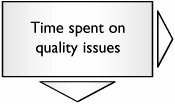 | By increasing the inherent quality level of the process, resource time could be freed up from scrapping, reworking, inspection and so forth. Go to Section C in this chapter to address this problem. | 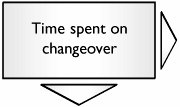 | By decreasing resource time spent on changeover, resource time can be freed up. Go to Section O in this chapter to address this problem. | 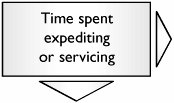 | By improving delivery performance, there will be reduced need for resources to be expedited or to make amends with the Customer. Go to Section A in this chapter to address this problem. | 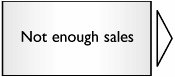 | If the base level of resource can support more sales, it will be worth spending time adding additional demand to the process. Go to Section V in this chapter to address this problem. |
|