For every task, there is more than one potential cause of a time overrun. When the project manager asks a team leader to give an estimate of the likelihood (Y) and the largest overrun time (D) for his or her task, the project manager reminds the team leader to consider as many potential overrun causes as possible. There is a tendency for a team leader to focus on one obvious potential overrun cause and not to consider others. The project manager will ask the team leader to begin by making a list of all potential causes of task time overrun that he or she can come up with. The team leader should ask task workgroup members and subject matter experts for help. Each potential task time overrun source will have its own unique overrun likelihood (Y) and its overrun duration (D). Experience has taught that the cause that produces the largest product of Y x D is the one that provides the contribution that best represents the task for the risk factor calculation. As the task leader reviews the various sources of potential time overrun, he or she also can easily consider what actions to take to mitigate this overrun problem if it is seen developing. As project manager, you should ask each team leader to make notes of the ways to mitigate time overrun problems and to be prepared to refer to them if necessary. Microsoft Project Management 2002® software and other software packages provide for a "Notes" record for each Gantt chart task. This record is a good place to store a task team leader's notes about what to do when problems arise. This type of thinking ahead is particularly valuable in long duration projects. The following is a sample list of frequently encountered task overrun causes: A team member is unavailable when needed. Some team members know less about performing their task than is expected. The equipment does not perform as expected. Resources are not available when needed. The supplier(s) does not deliver the necessary materials on time. Workgroup members have conflicts while working together and personalize them to the detriment of the task's progress. The task's output does not pass a performance test and must be reworked. There are many potential causes of task time overrun for every task. Most are particular to the type of task being considered. Purchasing tasks, for example, are particularly sensitive to having a supplier deliver a product of an inferior quality. A task leader, when reminded to do so, can create a good list of overrun causes for his or her task. After the task leader completes this list, he or she estimates the Y and for each overrun cause. If unavailability of a key task team member is a potential problem, the task leader must consider why this might happen. Is there a significant likelihood that a key team member will become ill? Is there a significant likelihood that a team member will be transferred or leave the company? If one of these things happens, what can the team leader do about it and how much delay will be caused by making adjustments? Careful consideration of this potential overrun cause might lead to the conclusion that there is a 20 percent likelihood (Y) of this problem emerging and a five-day worst case delay (D) associated with this cause. This same analysis may lead the task leader to decide that he or she needs a substitute list to back up his or her team members and to make such a list to include in the task "notes." Another potential cause of task delay for this same task might be that some task members do not have the expected skills. Many projects involve tasks that are familiar to some team members but are new to others. Because estimates tend to be based on the capabilities of experienced workers, it is important to focus on the limits of those who are inexperienced. Making estimates of a possible overrun for such a situation is a challenge for a task workgroup leader. He or she should discuss it with subject matter experts whenever possible. If several members of his or her task workgroup are inexperienced, he or she probably will be generous in estimating the likelihood of task time overrun. In considering what to do about it, he or she probably will include obtaining coaching help from specialists outside the task workgroup and record in the notes the names of specialists that can be approached for help. The amount of time it could take to help inexperienced workers get their job done may cause the task leader to use a generous amount of D. Facility availability may be easier to estimate because it generally has a long history. The facilities manager can help the task leader with this estimate. This style of analysis must be conducted for every condition that the task leader considers as a potential source of overrun. To select the proper contribution from his or her task to the risk task, a task leader should use the worksheet illustrated in Figure 9-1.
Figure 9-1. 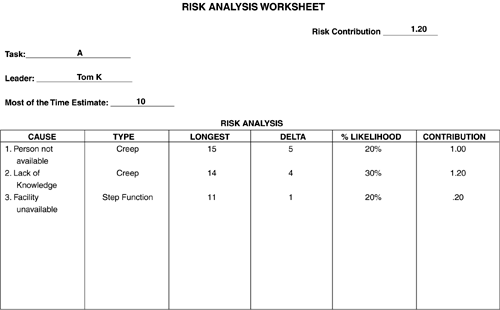 In this figure, the unavailability of a task member has a 20 percent likelihood of impacting the task and, as a worst case, could cause a five-day delay. This is a creep type of delay because there is a much greater likelihood that a team member would become sick and cause a one or two-day delay than a team member would leave the company and cause a five-day delay while he or she is being replaced. The contribution that this delay would make to the risk factor calculates as 0.2 x 5 = 1.0, or one day. Lack of knowledge and skills among team members is considered to have a 30 percent chance of impacting the project because one team member has a limited background in the type of work he or she will be doing. Although he or she is conscientious and bright, and the project leader expects the worker to work well with the team, there is still a possibility that an outside subject matter expert will need to be brought in to coach this worker. This may delay task completion, in the worst case, for four days. It is a creep type of risk, and the contribution from this cause is 0.3 x 4 = 1.2 days. Another potential source of task delay might be the unavailability of a test facility. This happens about 20 percent of the time. When it does happen, the team must wait one day to complete its work. This is a D of one day, and it is not a creep risk. If there is any delay, it is going to be a full one day. Do not try to combine this information to determine a task's risk factor. We have tried it. It is awkward and does not provide a good contribution number. You should pick the largest contribution from the list of potential overrun causes and use that number, in this case 1.2 days, for the task's contribution to the risk factor. There is a one-day step-function risk that you would report to the project leader separately if it were bigger than the calculated contribution. In this case, however, it will not impact the calculation of the risk factor and does not need to be noted. If there is a step-function D that is bigger than the calculated contribution, you should report this to the project manager for attention when combining contributions to determine the risk factor. If it turns out that the step-function is large greater than 50 percent when compared to the risk factor for the task sequence that is calculated, the project manager will lead the team in using the following formula: D - 50% of Risk Factor = Risk Factor Adjustment. |