To best prepare for exam questions on quality planning, you need to understand some key quality management principles and the PMI quality management philosophy. Specifically, you should be able to answer the following questions: What are the key PMI quality principles and how does PMI define quality? In what ways are quality management and project management similar? Who has responsibility for quality? What are the costs associated with quality? How does quality management impact project success? What are the differences among quality planning, quality assurance, and quality control? Who are the pioneers in quality management and what are they known for? Key PMI Quality Principles The PMI quality management philosophy is a generalized approach that remains consistent with the industry quality standards (such as ISO 9000 and ISO 10000) and popular quality methodologies (such as Total Quality Management, Continuous Improvement, and the Deming Cycle). To PMI, quality equals "conformance to requirements and fitness of use." Simply translated, this means that the project produces what it said it would, and that what it produces satisfies real customer needs. Here are the key principles to remember about the PMI quality management approach: Quality is doing what you said you would do. Quality is planned in, not inspected in. Quality is "prevention over inspection." Quality management addresses both product (goods and services) quality and project management quality. The project manager has ultimate responsibility for the project product quality. Effective quality management is consistent with effective project management. A work package should be verified and tested before submission. 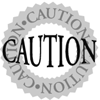 | PMI also emphasizes that quality is not giving the customer "extras" or doing more than promised. PMI refers to this practice as "gold plating" and consistently discourages it. |
 | Memorize PMI's definition of quality: "conformance to requirements and fitness of use." |
Similarities Between Quality Management and Project Management As mentioned before, PMI believes strongly that there is a natural partnership between effective quality management and effective project management. To better illustrate this, the following list highlights the similarities between the two disciplines: Both focus on customer satisfaction. Both generate requirements from customer needs. Both focus on the project accomplishing its goals. Both emphasize prevention over inspection. Both emphasize accountability. Both emphasize activity verification. Both leverage lessons learned from the past. Both use processes within phases. Both advocate management responsibility. Both focus on keeping the project on schedule (to avoid the temptation to sacrifice quality steps in the interest of meeting target dates). Finally, the project manager has the ultimate responsibility for the product quality and project management quality for the project. Quality Responsibility Per PMI, the project manager has the ultimate responsibility for the product quality of the project. However, he or she shares the responsibility for quality with the sponsoring organization and other project team members. Refer to Table 5.6 for a summary of the project quality responsibilities. Table 5.6. Summary of Project Quality ResponsibilitiesStakeholder | Quality Responsibility | Notes |
---|
Senior management | Has the ultimate responsibility for quality in the organization | The entire organization has quality-related responsibilities. | Project manager | Has the ultimate responsibility for the product quality of the project | Establishes quality procedures for the project. | Individual team members | Responsible for self-inspection | Work should be verified and tested before submission. | Quality Costs Another attribute of quality management that is consistently tested on the exam is costs. As reported in the PMBOK, 85% of the costs associated with quality management is the direct responsibility of management (both project and senior). For the exam, you need to understand that there are three types of quality costs prevention, appraisal, and failure and that costs are associated with conformance to requirements, as well as with nonconformance to requirements. Table 5.7 summarizes these quality cost categories. Table 5.7. Summary of Project Quality Cost CategoriesCategory | Type | Examples | Impact on Project |
---|
Conformance | Prevention costs and appraisal costs | Cost of quality management, quality training, studies, surveys and inspections | Increased productivity, increased cost effectiveness, and decreased cost risk | Nonconformance | Failure costs; internal and external | Rework, scrap, inventory costs, warranty costs, and goodwill costs | Increased costs, lower morale, lower customer satisfaction, and increased risk | The Differences Among Quality Planning, Quality Assurance, and Quality Control To better understand the role of quality planning in the quality management process, it is important that you review how this step fits in with the other quality management processes. In addition, because many project managers have not had extensive experience with disciplined quality management, the distinctions between the processes are not always obvious. To bring clarity to these matters and to help prepare you for the exam, Table 5.8 details the differences among quality planning, quality assurance, and quality control. Table 5.8. Key Differences Among Quality Planning, Quality Assurance, and Quality Control | Quality Planning | Quality Assurance | Quality Control |
---|
Process Group | Planning | Executing | Controlling | One Word Description | Plan | Implement | Measure | Key Questions | What quality standards apply? How will we meet those standards? | How can we improve quality? Are the standards still appropriate? | Did we meet the specific standard? What are the measurements? | Key Output | Quality management plan | Quality audit results and quality improvements | Inspection results and corrective actions | Quality Pioneers Frequently the exam will reference material outside the PMBOK for quality management related questions. A common technique is for the exam not to ask specifically about this "outside" material but rather to mention this material as part of the project context with the assumption that you know what the exam is talking about. If this assumption is not true, you'll find yourself less than confident on those questions. To assist in this area, we summarize the key facts regarding the pioneers of the quality management field in Table 5.9. You can count on references to one or more of these guys on an exam question. Table 5.9. Pioneers of Quality Management SummaryPioneer | Best Known For | Notes |
---|
Dr. W. Edwards Deming | The Plan-Act-Do-Check Cycle The Deming Cycle | The cycle is repeated within a phase, much like the project management processes. | Dr. Joseph Duran | The Duran Trilogy: quality improvement, quality planning, and quality control The Ten Steps to Quality Improvement The concept of "fitness for use" | Quality is the set of product features that meets the needs of the customers and provides the most satisfaction. | Philip Crosby | The Fourteen Steps to Quality Improvement The Four Absolutes Meeting all requirements Error prevention Zero defects Done right the first time | Focused on the consequences. Doing the right thing properly the first time is less costly. |  | Exam questions concerning quality management frequently reference material outside the PMBOK. |
|