The Gantt chart timeline is the primary tool for monitoring and managing a project and its cost. This completed chart clearly defines the project's timeline, but its cost is not obvious without additional processing. Before software, developing the cost of a project was tedious. A procedure using the Gantt chart for cost projection is attributed to Robert MacNamara, former analyst of the Ford Motor Company. MacNamara's procedure has been incorporated into project management software. Because the Gantt chart depicts effort and other resource requirements, the budget can be created by applying rates to effort and unit costs to the resource units. MacNamara's cost method is illustrated in the toy truck example (see Figure 10-3). Inserting a resource cost table under the task list provides a day-by-day and task-by-task cost reference. Purchasers (P), Carvers (C), Machinists (M), Assemblers (A), and Helpers (H) are paid at a rate. With their tasks noted in days, entering the daily rate is essential.
Figure 10-3. 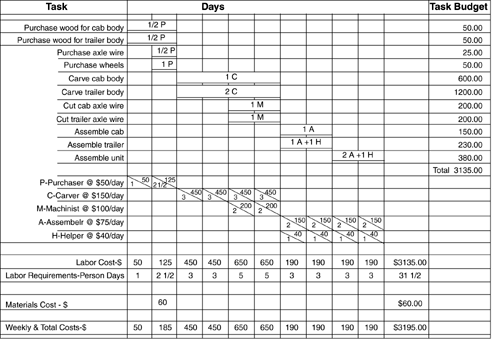 In this example, letters represent the type of workers used in a task, and fractions or whole numbers represent the amount of time a particular type of worker is committed per day for the task. Thus, on the task row "Purchase wood for cab body," the bar covering two days shows the task duration, and the symbol 1/2 P signifies that each day of the task one purchaser will be working half of the time. "Purchase wheels" is a one-day task; 1 P written within the task bar indicates that for one day a purchaser will work full time at this task. The "Carve the trailer body" task is four days long. The 2 C entry indicates that the two carvers will each work full time on this task for all four days. Below the body of the Gantt chart is a list of entries that are the forerunners of the resource table screens used in modern project management software. The column lists each type of worker who works on the project and his or her daily rate. Each type of worker who works on a task on a particular day is identified, and the fraction of time he or she works on a task this day is noted by the cost analyst. Worker time then is added up for each day. Reading down column one (Day one), two tasks are being executed that day. On each task, a purchaser (P) is working half of the time. Two purchasers working half of the time each is the equivalent to one purchaser working full time. Note that the cell indicating a day on a worker row (Purchaser) is divided into two parts by a slash mark. The full-time equivalent of purchasers working on Day one is one. On the Purchaser row, one (1) is entered in the lower portion of Day one's cell. To determine the cost of the purchaser's effort for this day, the analyst multiplies the figure in the lower half of the cell by the rate shown beside the Purchaser's name, (that is, $50). Multiplying the number of full-time equivalent purchasers working this day by the purchasers daily rate(1 x $50) produces the cost number for the upper part of this cell: $50. Each day column is treated this way for each type of worker who is working that day. Thus, on Day two there is a full-time equivalent of 2 1/2 purchasers working: $50 x 2.5 = 125. The purchaser labor cost for the second day is $125. On Day five, carvers and machinists are both working. There are three carvers working at $150 per day each. On the Carver row of column five, the number 3 is entered below the slash line. At a rate of $150 a day, three carvers add $450 to the project's cost on that day. On the same day, there are two tasks, "Cut cab axle wire" and "Cut trailer axle wire," each with a machinist working full time. Therefore, there are two full-time machinists working that day. The cost analyst enters the number 2 on the lower part of that day's machinist row cell and 2 x $100 = 200 in the upper part of the cell. The cost per day is arrived at by totaling the dollars listed for that day. Labor, in persons per day, is determined by totaling the number of workers who are listed that day. Material costs are entered when purchased materials are delivered. Wood for the cab body, wood for the trailer body, axle wire, and the wheels are all delivered on Day two. Each item costs $15. The cost analyst totals this up and enters it in the Materials Cost row in the cell for the second day: $60. In this way, all costs for the project can be captured and totaled. The cost analyst is interested in the cost for each task. To determine it, he or she notes the full-time equivalent of the workers in each category who work on each task. He or she then multiplies the worker days by the worker rate and adds them together to determine the task cost. For example, the "assemble trailer" task requires two days of effort from an Assembler: 2 $75 = $150, and two days effort by a helper: 2 x $40 $80. The labor cost for that task is $150 + $80 = $230. (Note: This example and the rates here are taken from an old example, but they were very good rates when McNamara worked at Ford.) The principles previously described have been written into project management software. Details are embedded in the software but are not displayed as shown in the longhand example. The software, nevertheless, follows and expands upon this formula. If resource cost information is entered on the resource cost screen, the software automatically can calculate and print the cost projections from the Gantt chart information. As previously noted, before building the Gantt chart, the project manager should enter the anticipated cost of the resources (persons and materials) on the software resource cost screen. It is not crucial, however, that all resources and costs be entered before the Gantt chart is constructed. Microsoft Project 2002® and other packages automatically will list the resources on the resource screen when task resources are entered on the Gantt chart. When resource cost information is entered later, cost projections then can be displayed and printed out. When resources are identified as people and their names are used, some people may not want their individual rates published. If so, the project manager can get the average rate for this person's category from accounting and simply use that figure. |