T. Waste/Process Loss Too High Overview Common to most industrial processes, where materials are processed in multiple steps from raw materials through intermediates to finished goods, there are opportunities to lose molecules of product throughout the process.[15] The objective of this type of project is to minimize the loss from the process. [15] This is especially common in chemical and pharmaceutical processes. Examples Measuring Performance Process loss is measured using a mass balance equation, such as 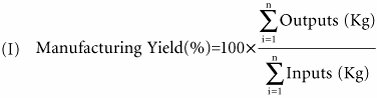  where Outputs are the finished product exiting the process. Inputs are the components and raw materials entering the process. Stock is the inventory of materials through the process. Tool Approach 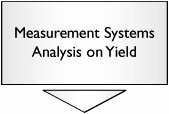 | Initially, the focus is on measuring Yield (from equation I), so the ability to identify Mass In and Mass Out will be important. At this stage, the interest is only at the high level in the ability to identify what the business thinks is the mass of raw materials purchased and the mass of finished products shipped. This will just be a validation at this point, and not a Gage R&R Study on the weigh-scales, for example. For more details see "MSAValidity" in Chapter 7, "Tools." | 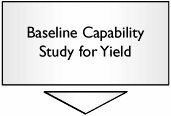 | For the Yield as validated in the preceding MSA, take a baseline measure for a period of one month or more. This data will almost certainly be available historically. | 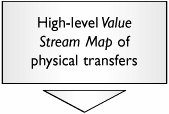 | Construct a high-level Value Stream Map highlighting in particular any physical transfers of material, or points where material loss could occur. Any low-cost, low-risk, quick-hit opportunities should be taken at this point. | 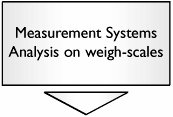 | The Team will need to collect loss data throughout the process, so for each measuring device (scale, weigh-counter, etc.) there should be an up-to-date MSA. This should be a full Gage R&R Study. For more details see "MSAContinuous" in Chapter 7. |
The majority of unaccounted loss is typically at the beginning and end of a process, so the focus should be here first. 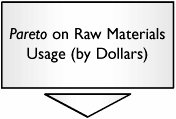 | Taking Raw Materials and components first, the approach will be to identify process loss using a Capability Study. However, given that there are probably large numbers of Raw Materials, a Pareto will provide a prioritized approach. A Pareto by dollar value for usage rates will be best because the focus is on cost reduction. | 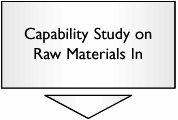 | Stated and actual content of purchased containers invariably differ significantly. Even though it might state 2.5Kg on the container from a supplier, it is highly likely that the material content will differ from this amount, often representing significant loss (and less frequently gain) in the process. Using the prioritized order from the Pareto, examine the capability of actual versus stated contents of containers. Use a normalized scale with zero being the correct content, underfill the negative content, and overfill the positive content. For more details see "CapabilityContinuous" in Chapter 7. This is best done as the materials are being used by the process. Twenty to thirty data points will be required for each component, so this will be quite a lengthy undertaking. | 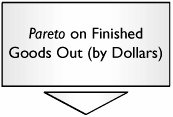 | Next, take a similar approach for the Finished Goods. Construct a Pareto of the finished (and shipped) goods by cost. | 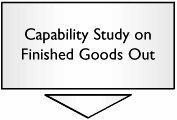 | Starting at the top of the Pareto of Finished Goods Out, examine stated versus actual contents. Log any significant deviations. A quick hit here would be to mend the filling equipment or system. Overfilling can account for as much as a 5% material loss. | 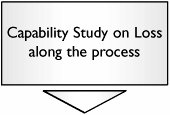 | The most significant losses are usually at the front and back end of the process, but measurements taken at key points along the process can identify potential high-loss areas. Measure mass transfer step by step along the process. |
After the losses are identified through the process and any quick hits eliminated, the roadmap should be to use the equation Y=f(X1, X2,..., Xn), where the Y is the process loss, measured in units of mass. to find the key Xs that minimize the Y. Go to Section C in this chapter. |