Overview[1][1] Before reading this chapter it is important to read and understand Chapter 1, "Introduction," particularly the section, "How to Use This Book." All projects, regardless to which Problem Category they relate, progress through the same series of tools at the back end of the project (the late Improve phase and through Control to Validation and Signoff). The purpose of this part of the roadmap is to ensure: The process is clearly defined and laid out. The process control mechanisms are in place. The process is done consistently. The process roles are defined along with associated competences. Process documentation is complete and up to date. Process staff are maintained at the right competency level. All of these ensure the process performs at the new, elevated rate for all time. A project signoff is done to demonstrate performance and its significant difference from the baseline. Tool Approach The primary deliverable of any project is the Control Plan. The Control Plan represents all the elements that must come together to control the process so that it performs at the desired level for all time and comprises Critical Parameters. The key performance characteristics (Ys) by which we measure the process, along with the identified key Xs that drive the majority of the variability in the Ys. Measurement Systems Analyses. Demonstration of the ability to measure the Critical Parameters. Capability Studies. For Critical Parameters that demonstrate performance to requirements. Reaction Plans. For the Critical Parameters if they fail to meet performance requirements. Control Plan Summary. A single form that documents the summary of the above elements. Customer information. The levels, profiles, and segmentation of demand that the process experiences. Process Maps. The definition of the process and its flow. Standard Operating Procedures (SOPs). Documentation reflecting how the process should run Failure Mode & Effects Analyses. A history of the risk in the process and how it has been reduced. Continuous Improvement Plan. Accountability and approach for improving the process (or mending it if it breaks). Training materials and methodology. The tools to bring the operator competences to the levels required to run the process. Maintenance. Ongoing maintenance requirements to ensure the process sustains its performance improvement. The Control Plan ensures that all the elements listed in the overview at the beginning of this chapter are considered. The following roadmap lists a linear sequence of events that construct the Control Plan and lead up to the signoff of the project. In reality, steps overlap at times and minor refinements can be made to earlier steps after the later work is finished. The sequence of completion is fairly consistent though. The new process must be clear enough and defined to the point where it can be, or has already been, implemented. The best tool for this purpose is a Swimlane Map because it clearly defines sequence of activities by role. 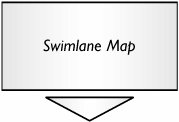 | Use the Swimlane Map to demonstrate visually how the new process runs and how the roles relate to the process steps. |
After this is complete, the Team needs to build in the controls on the critical Xs identified through earlier parts of the roadmap. 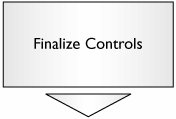 | There are a number of options available to maintain control on an X. In descending order of strength, they are Design out the X completely. For example, if the operator is the critical X, can we automate the step so that there is no operator involvement? Mistake-proof the X so that it cannot be changed inappropriately. This is sometimes known as Poka Yoke. For example, for key knobs on machinery, screw the knob down so that it cannot be changed or consider removing it entirely. Use Statistical Process Control at the workstation to ensure that if the X goes out of control, then it is identified and the appropriate responses are made. Post Parameter Cards at the workstation to ensure operators know at what settings to run the Xs. Train operators how to maintain the Xs at the prescribed level. Some combination of all of the above is usually done.
|
At this point, it is worth reexamining the triggers that ensure each activity begins correctly. These might be some of the key Xs, but this is important to do for the whole process. Triggers are known as Kanbans in the Lean Sigma world and ensure that Pull is occurring through the process; for example, when you are free to work on something, you have something to work on, unless there is no demand from the Customer. See "Pull Systems and Kanban" in Chapter 7, "Tools," for more detail. 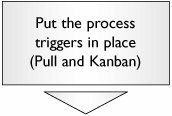 | For key points in the process, it is necessary to have signals to upstream steps that subsequent steps are ready to work; for example, in an Operating Room a trigger might go out to feeder processes that the current Patient procedure completes in 10 minutes. This allows the next Patient to be prepped and so on. This is a Pull System and the trigger is known as a Kanban. Without these, time is lost in the process when entities stall due to lack of readiness. |
After the process is defined, it is possible to examine its layout. There are many tools available to aid in this endeavor, such as Cellular Design and Workstation Design. They are not covered here due to the sheer volume of options available, but at this point, the process needs to be laid out correctly based on the business and process requirements. 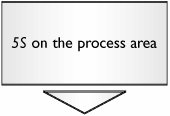 | Based on the process layout chosen, the materials, supplies, and so on, need to be organized appropriately. 5S helps immensely here. |
After you define the process, determine the triggers, and lay out and organize the process, the focus becomes ensuring that the process runs like this for all time. The beginning of this is known as Standard Work 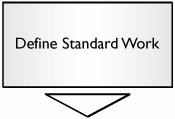 | Standard Work is the formal documentation of a group of tools that helps define the day-to-day running of the process. It is made up of Takt Time (the pace of market demand) For more details see "TimeTakt Time" in Chapter 7. Process Cycle Time (the pace that the process runs) For more details see "TimeGlobal Process Cycle Time" in Chapter 7. Total Work Content (how much labor time is involved in each step) Load Chart (graphical representation of Takt versus Cycle Time) Layout of the process Order of the process Work sequence (and timings) for the operators Work sequence (and timings) for any equipment/machines Standard inventory in the process
|
After the Standard Work is defined, the process can formally begin to perform in its newly prescribed way. To do this the Team needs to set the key Xs to their correct level. [Pages 112 - 113] 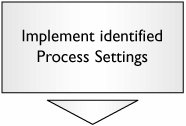 | For the critical Xs, the levels determined earlier in the roadmap must be set in place. The formalized controls will also be implemented on these Xs at this time. For non-critical Xs, Team focus is on choosing the most appropriate (usually economical) settings. | 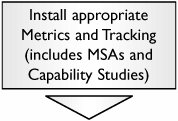 | The key tracking metrics for the process will be the Ys and critical Xs. For each, if not already done so, a Measurement Systems Analysis will be required. For more details see "MSAValidity," "MSAAttribute," and "MSAContinuous" in Chapter 7. For each MSA, a regular revisit schedule is also required. After the Measurement Systems are deemed fit (the Team must mend them if not), then initial Capability Studies are made. Ideally on-line tracking is instigated or worst-case a schedule is set up to revisit Capability on a regular basis. | 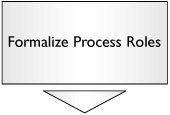 | For each role defined in the process, a role checklist or documented approach is createdin effect a "how to do the role." Note that sometimes there is confusion between people and roles. A role is the "chair to sit in"; a person is the "one that sits in the chair." Roles remain; people can come and go. | 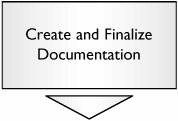 | Construct documentation for the process as a whole. The best documentation involves visuals, so rely heavily on Swimlane Maps and so on. Remember to include detail of key Xs, metrics, tracking, and reaction plans (these are sometimes overlooked). | 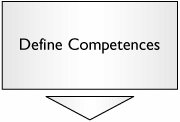 | For each role in the process, the Team identifies the competences required to perform the role; think of this like a license. These competences must be written in objective language and their attainment should be readily measurable.[2] | 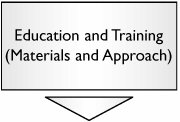 | For each competence there needs to be provision of education and training to attain this competence. The actual training is not conducted at this point. | 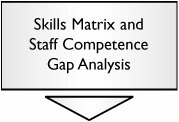 | Finally, the existing staff is layered back onto the process by examining their competences. The matrix of staff versus competence is known as a Skills Matrix. The tendency here is to overdo it and break out every tiny skill. The best approach is to keep it grouped to a maximum of 30 to 40 skills across the process or the Skills Matrix becomes too unwieldy. | 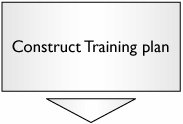 | The Skills Matrix is in effect a large Gap Analysis on staff competency. From this, the Process Owner (not the Team) must construct the training plan to bring the staff up to the required levels. This might involve recruitment. | 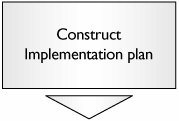 | Often the solution created is for a single line or entity type and there needs to be a rollout to other lines or entity types. A simple Milestone Plan helps communicate the rollout and improve the likelihood of a timely implementation. | 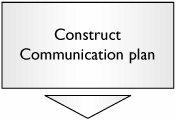 | Most processes involve stakeholders who need to be informed of the impending changes. Constructing a Communication Plan ensures the appropriate parties are well informed. | 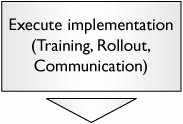 | The actual rollout might or might not be considered part of the Lean Sigma project but is required by the business. (Signoff for the Lean Sigma Project could be based on the pilot process success.) It might be necessary to form separate implementation teams to take the changes to the rest of the organization. | 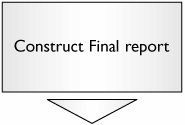 | At first glance, the creation of a Final Report might seem like NVA work, but it is important to maintain organizational learning with respect to the project. In future projects, Belts will be able to refer back to the work done here and hopefully avoid unnecessary pitfalls. | 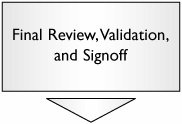 | Validation is data-based and should be justified by a t-Test, usually a 2-sample t-Test, or similar to show that the changes made to the performance metrics are statistically significant. For example, that the gains are real. Reviewers should include the Champion, Process Owner, and a technical resource (Master Black Belt). The signoff represents the project coming full-circle and the final handoff to the Process Owner is complete. |
[2] The most common system is known as a 5-Star rating and uses five levels of attainment of competence, usually from "No Knowledge" through "Awareness,""Has Been Involved," and "Led" up to "Can Teach Others." All that is left is the important celebration of the results. Remember to include all those involved in the success of the project. Then take a break; the next project will be along shortly... |